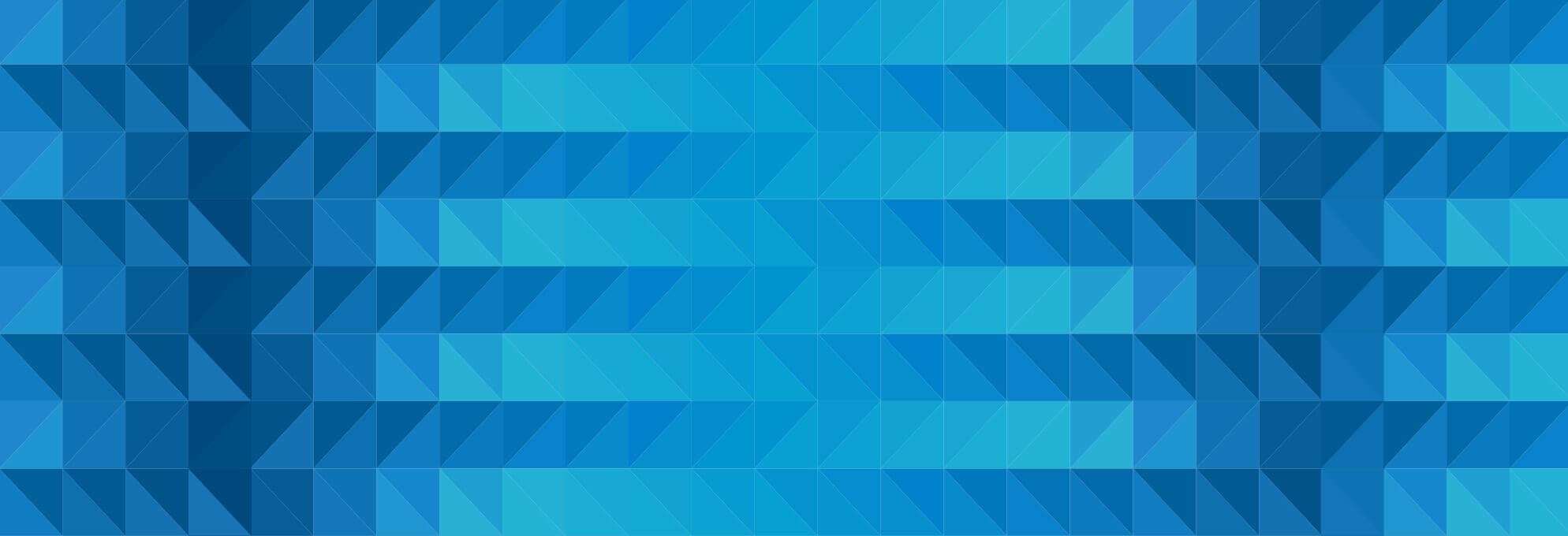
PDA Visual Inspection Forum 2025 Posters
Poster Summary/Abstract Information
-
Leveraging Deep Learning and AI-Driven Facial Tracking Systems to Enhance Manual Visual Inspection in Pharmaceutical Manufacturing
My experience in pharmaceutical manufacturing showed me how vital manual visual inspection is, but it also highlighted a common challenge—sustaining operator focus over long shifts. I wanted to develop a tool that supports both operators and quality teams by providing objective data on attentiveness. The goal is not to ‘catch mistakes’ but to help companies create smarter inspection programs—like optimizing shift lengths, break schedules, or rotation plans—to ultimately reduce errors and improve product quality.
Our system helps companies understand when and where attentiveness dips during inspection shifts. With this data, they can make informed adjustments—like adding short breaks at strategic times or rotating operators—to ensure consistent inspection performance. By providing real-time feedback to operators and supervisors, the system promotes engagement and helps prevent fatigued decisions, leading to more robust quality control processes and fewer defects escaping into the supply chain.
“Poster presentations create an open environment to exchange practical solutions with others in the industry. They encourage conversations that go beyond theory—allowing professionals to discuss real-world challenges and collaborate on ways to strengthen quality systems. Presenting innovations like ours opens the door to gathering feedback from peers and learning how tools like facial tracking can integrate into diverse inspection processes across different companies.My near-term goals based on this poster innovation:
- Conduct pilot programs with pharmaceutical manufacturers to demonstrate how attention data correlates with inspection performance over a shift.
- Work alongside quality teams to analyze this data and co-develop improved operator schedules, break structures, or task rotation plans based on attention patterns.
- Build case studies showing how data-driven adjustments lead to better inspection consistency and fewer escapes, without increasing operator burden.
- Explore partnerships with inspection equipment providers to offer our system as an enhancement tool that supports operators rather than replacing them.
Refine the system based on real-world feedback to balance attention monitoring with maintaining operator comfort and trust.
Ali Yuksel
Managing Partner | Principal EngineerYBAbstract
Download PosterIn pharmaceutical manufacturing, visual inspection is critical for ensuring product quality and safety. Manual inspection processes, however, can be compromised by human error and operator inattention. To mitigate these challenges, we propose an AI-driven facial tracking system that leverages deep learning to enhance operator attentiveness during manual and semi-automated visual inspections.
Our system uses facial recognition and gaze tracking algorithms to monitor the operator’s focus in real-time. By detecting facial landmarks and tracking eye movements, the system assesses the operator's attention level. If lapses in attentiveness are detected, the system triggers interventions such as visual or auditory alerts, conveyor pauses, or notifications to supervisors, ensuring continuous operator engagement and improved inspection reliability.
This adaptable and scalable system integrates seamlessly with existing workflows, significantly reducing the likelihood of missed defects due to inattention. By incorporating AI and deep learning, the system substantially improves product quality assurance and regulatory compliance, ultimately reducing human error in pharmaceutical visual inspections.
This abstract presents a novel approach to using deep learning and AI to optimize visual inspection processes, helping to ensure higher quality control standards in pharmaceutical manufacturing.
-
Test Kit Fabrication Lab
I have been responsible for visual inspection for the majority of my 25-year career in multiple roles. I have a passion for visual inspection and the qualification of inspectors and equipment. I know the baseline for a robust qualification program starts with realistic, challenging defect test kits.
I am currently the Manager of a newly created Test Kit Fabrication Lab, and I want to share some of the benefits we have seen since its implementation. We have seen real benefits associated with the capability to internally prioritize test kit creations. We have a very aggressive timeline with new product launches and facilities, and the ability for us to prioritize the kit needs of each line has enabled us to hit tight deadlines. With the internal lab we have also been able to create samples/kits for testing and to aid in investigations. My goal is to continue to pursue innovation in defect creation to further improve the quality and consistency of the test kits we produce.
Poster presentations allow us to share new concepts or new iterations of old concepts to individuals who are interested. It allows individuals attending the conference to discuss the concepts being presented with the presenter in a more informal setting outside of the larger group.
Christopher Barnes
Advisor -Global Visual Inspection StewardEli LillyAbstract
Download PosterDeveloping an internal visual inspection test kit fabrication lab and the positive results achieved post implementation. Discuss what went into the design of the lab from the brick and mortar space to the equipment we utilize to fabricate our defect sets. Discuss how the lab has enabled us to review performance across sites around the world and establish best practices for visual inspection technique and equipment. The lab has enabled us to move forward with a very aggressive manufacturing plan all while maintaining a quality qualification strategy for manual, semi-automated and automated inspection.
-
Challenges for Particle Control and Visual Inspection in Cell Therapy Products
Dr. Roman Mathaes
Chief Executive OfficerClear Solutions Laboratories AGAbstract
Cell therapy manufacturing presents unique challenges, including the absence of a final point of filtration process and manufacturing equipment ensuring sterility, however not optimized for low particle loads/shading as well as difficulties in discriminating particle impurities from the product (cells). The visibility of particles is strongly impacted by turbid cell suspensions during visual inspection.
The poster summaries challenges for particle control and visual inspection for cell therapy products and provides solutions to each challenge.
-
Redefining Visual Inspection Particle Detectability Limits for Standardized Operator Qualification
Filip Fedorowicz MSc
Associate Principal ScientistClear Solutions Laboratories AGAbstract
Download PosterThe definition of visible particle size which must be controlled and monitored during visual inspection remains a challenge to establish, with lack of very detailed guidance from regulatory authorities. Various sizes have been cited as thresholds of particle visibility; however, despite efforts on harmonization, a singular visibility limit for particles remains an elusive goal. Particle size, such as “Feret Max” or longest aspect ratio length, does not allow for single visibility limits due to diverse particle morphologies impacting detectability. Setting visibility limits is achieved by threshold studies or previous product knowledge and expertise.
This work proposes the usage of a particle size definition corresponding with human visual perception based on the equivalent circular diameter. Our findings provide evidence for obtaining single visibility limits for typical process related particles obtained from a threshold study with qualified operators. Additionally, we demonstrate that singular visibility limits are dependent on product and container characteristics, highlighting the requirements for product specific training and qualification using well designed test sets. These remain a crucial element in qualification of visual inspection systems as manual operator visibility defines the baseline in the qualification of automated vision systems.
-
A Comparison of Barrier Film Non-Stick Coated Stoppers vs. Non-Barrier Film Rubber Stoppers in Pharmaceutical Packaging: A Case Study from Historical Data
My poster presentation was inspired by an observation that a customer had regarding two of her projects. While performing a Knapp Study, visual inspectors were having difficulty finding all the particles in one project, and much less difficulty in another project. The customer asked us how this was possible since the projects were identical and we concluded that the stoppers that were supplied for the two projects were not the same, thus the particles had a higher chance of sticking to one stopper type than the other.
The information presented in my poster will show how the choice of stopper that is used in visual inspection kits may affect the usefulness of the kit over time. Poster presentations allow research to be synthesized in a visual format, and presenters can receive immediate feedback from their peers regarding their research. This practice aids in collaboration between members of the scientific community.
Heather Marzolo MS
Laboratory TechnicianSartoriusAbstract
Download PosterIn pharmaceutical packaging, the choice of stopper material can significantly impact product quality and safety. Additionally, the type of stopper material alters the efficacy of visual inspection training kits for qualifying visual inspectors. This study compares the performance of coated stoppers with a barrier film non-stick coating (Teflon®; FluroTec®, OmniFlex® barrier film) and non-barrier film rubber stoppers in identical projects to evaluate their effectiveness in training visual inspectors. Two identical projects were created, one using coated stoppers and the other using uncoated stoppers, with all other components being equivalent between the two projects. The coated stoppers were evaluated for a validity period of two years, and inspections were conducted to observe the presence of foreign material(FM) in both projects.
The results indicated that particles adhered to the non-barrier film rubber stoppers, which can prevent the particles from becoming free-floating. After the two-year validity period, particles were found to be free-floating in the coated stopper units and no additional FM was present in these vials.
Utilizing barrier film non-stick coated stoppers in visual inspection training kits and training inspectors how to use different lighting, angles, and tools to detect FM, enhances the overall inspection capabilities and consistency of the visual inspectors.
-
Relationships Between Visual Inspection Detectability and Liquid Extraction Measurement of Particulate Matter in Bioprocess Containers
Klaus Wormuth PhD
Principal ScientistSartoriusAbstract
Download PosterAlthough single-use bioprocessing equipment are often manufactured under controlled conditions in clean rooms, particulate matter may still be present on the inside (fluid-contacting) surfaces. Contrary to popular belief, the USP chapters < 788> and < 790> do not describe test methods for determining the levels of particulate matter in single-use bioprocessing equipment. In this poster, best practices for visual inspection and for the liquid extraction and measurement of particulate matter inside single-use bioprocessing equipment are described. The relationships between visual detectability and container plastic film and container complexity are compared to results obtained from the liquid extraction (destructive testing) and count/sizing /identification of particulate matter present inside the containers.
-
Different Types of Test Sets Throughout a Visual Inspection Project Lifecycle: From Vendor Selection to Visual Inspection in Production
At Eyetec we receive a lot of requests for the creation of test kits although customers are not always certain on what to include in them and what to look out for. This inspired me to create the poster presentation of ‘Different Types of Test Sets Throughout a Visual Inspection Project Lifecycle: From Vendor Selection to Visual Inspection in Production.’ My intent is to give a clear overview of all possible test kits. Bracketing or combining certain kits is possible as long as we ensure not to bias the process in either manual or automated inspection.
From selecting the right vendor and developing custom test sets to ongoing validation and production testing, each stage relies heavily on well-designed test sets to meet quality standards and improve the overall process. The poster aims to highlight the importance of understanding how different types of test sets are utilized at each phase of the visual inspection lifecycle. By breaking down these phases, I wanted to emphasize the step-by-step approach needed to maintain high-quality inspection processes and ensure consistency and reliability in production environments. The combination of these concepts creates a more holistic view of visual inspection projects, offering valuable insights for professionals looking to optimize testing strategies and achieve better results.
Clearly mapping out the different types of test sets throughout a visual inspection project lifecycle will enhance the industry by providing a structured, comprehensive approach to managing and optimizing visual inspection processes. Here's how it can contribute:
- Improved Accuracy and Reliability: By understanding and using the right test sets at each phase (from vendor selection to production), companies can ensure their visual inspection systems are working in a correct manner.
- Streamlined Workflow: Breaking down the test sets into specific phases allows organizations to streamline their workflow and avoid inefficiencies. It guides professionals in selecting and applying the most appropriate test sets, which can lead to faster implementation and quicker adaptation to new inspection systems.
- Cost Savings: Proper testing early in the process can catch defects or performance issues before they reach full-scale production. This prevents costly rework or product recalls, thus saving the company money in the long run. By applying the right test sets, the industry can achieve more reliable inspections with fewer resources needed for troubleshooting.
Overall, this approach can contribute to higher operational efficiencies, greater product quality, and more informed decision-making benefiting the industry by enhancing both the technology and processes behind visual inspection systems.
Poster presentations are important because they provide a clear, visual way to communicate complex information in a concise format. They allow for easy sharing of ideas, foster engagement with the audience, and encourage discussion. They are also an effective tool for showcasing research or innovations in a way that is both informative and accessible.
My near-term goals based on the poster innovation are to raise awareness of the importance of structured test sets in visual inspection, promote best practices in the industry, and collaborate with vendors and professionals to refine inspection processes for better accuracy and efficiency.
Menno Sels MA
Senior Process & Project EngineereyetecAbstract
Download PosterThere are multiple defect testkits that can be used throughout a visual inspection project timeline. This posters summarizes all possible types of testsets: initial defect kit for treshhold study for the manual baseline, kits for feasibility studies for vendor selection, evaluation study kit for the selected vendor, mechanical testkit, FAT/SAT kit, Engineering run kit, PQ kit, PPQ kit & kits for during production activities (final functional kit & requalification kit).
This summary also points out what to look out for during defining the kits through a VI project + give some input on different strategies that are possible regarding the number of testkits + it’s composition. It’s possible to reduce the testkit effort & costs by combining kits at some stage. Also bracketing can be considered, in case of multiple products.
-
Linear Inspection of DIPs – A Valid Alternative to Conventional Inspection Methods for the Inspection of Lyophilized Products in Vials
Our poster reveals how linear-designed devices manage without formatted parts and work more efficiently than conventional rotary machines. In addition, a wide range of detection technologies that are developed and manufactured in-house can be integrated into these modular systems to ensure that even difficult-to-inspect products. For example, vials filled with loyphilisate can be inspected precisely and seamlessly. Products that cannot be reliably administered are reliably withdrawn from circulation before they reach the patient.
We tried to clearly visualize the typical defects of difficult-to-inspect products and highlight special detection methods such as our pulsed X-rays or our multi-color image processing for greater detection accuracy in camera-based quality inspection, while also incorporating our corporate design. Questions and answers in the text provide enlightenment about the background, challenges, applicable technologies and modules as well as their possibilities regarding the strictly linear in-line inspection of vials filled with lyophilised products.
The modular HEUFT spotter II PHS is the only vial inspector of its kind to feature both sophisticated optical detection methods with ingenious illumination and intelligent image processing procedures as well as our pulsed X-rays for reliable glass-in-glass detection. Foreign objects are identified gently and reliably, even if they are hidden inside the product. A headspace analysis to identify excess oxygen in the vial can also be carried out in a single operation. In addition, the compact linear system detects glass defects, contamination and fill volume deviations in full vials holding between 2 and 100 ml and precisely examines the container closure integrity. Even in the most confined spaces, a gapless complete inspection is possible with high line efficiency for comprehensive patient and brand protection. This makes it a real game-changer.
Posters are valuable when it comes to illustrating abstract content and summarizing important core messages. With this format, the technical features and advantages of our innovative in-line inspection solution are visible at a glance and hopefully also make a more lasting impression than would be the case with a verbal presentation.
Moving forward, I would like to increase the popularity of the inspection system we have developed and manufactured to create awareness in the pharmaceutical industry that such a multifunctional compact solution with an efficient straight-through design even exists. Up to now, we have mainly been known in the food and beverage industry as a technology leader in in-line quality inspection. I would like to change that. And the PDA Visual Inspection Forum 2025 is an ideal platform for doing so.
Sebastian Mayer
Product ManagerHEUFT SYSTEMTECHNIK GMBHAbstract
Download PosterThe inspection of difficult to inspect products (DIP) such as lyophilized parenterals is a challenge due to various influencing factors such as the glass quality, the composition of the material and the resulting optical properties. With these products, the conventional rotation approach does not offer any advantage and is unnecessarily complicated. The use of novel inspection methods specifically tailored to overcome these difficult optical properties can allow for reliable detection of faults that would have previously faded into the background noise. The use of multi-colored illumination in combination with different lighting principles in one inspection image makes it possible to highlight special defects but also to neglect common container structures.
In addition to optical camera inspection, other previously invisible defects in the lyo cake, such as glass fragments or metal particles, can also be made visible using pulsed X-ray technology.
-
Inspection Efficiency Through Regulatory Data Intelligence
Zephaniah Odidika
StudentThe Cooper UnionAbstract
Download PosterThe presentation will explore how these methodologies enhance inspection processes by identifying key compliance trends and supporting both automated and manual visual inspections. Specific applications include AI-driven optimization of inspection recipe development and strategies for manually inspecting difficult-to-assess parenteral products. Additionally, the research emphasizes the integration of regulatory intelligence into VI systems to address new compliance challenges.
Key findings include:
- Analysis of warning letter and 483 issuance rates by topic and category, showcasing regulatory focus areas.
- Comparative insights into geographic trends and newly developed segmentation techniques for the FDA’s regulatory dataset.
- Data and Charts pertaining to core conference topics such as visual inspections.
- This work demonstrates how data-driven insights can empower firms to optimize visual inspection workflows and adapt to the rapidly changing regulatory environment, ultimately advancing product quality and compliance outcomes.
-
Class-Conditional Vial Image Generation Using Diffusion Models for Enhanced Visual Inspection
Zhengqi Gao PhD
Phd studentMITAbstract
Download PosterThis abstract introduces a novel application of diffusion models for class-conditional generation of vial images to enhance automated visual inspection processes in pharmaceutical manufacturing. Utilizing a training dataset containing images of both good and defective vials, a diffusion model with a U-Net backbone was developed to generate high-quality, class-specific synthetic images. The diffusion model leverages the unique capability of generating realistic and diverse image variations conditioned on the class label, allowing it to simulate a wide range of defect types. This approach addresses a critical limitation in automated inspection systems—the lack of extensive, balanced datasets with sufficient defect coverage. The generated synthetic data can augment existing training datasets, facilitating the development of more accurate defect detection algorithms and enabling comprehensive validation of inspection tools. Additionally, this work supports risk-based validation efforts by simulating edge cases and rare defects that may not be adequately represented in real-world datasets. The implications extend beyond defect detection to improving the reliability of automated inspection systems and accelerating the implementation of innovative inspection processes in the pharmaceutical industry.